INDEX
製造業・生産管理では、生産管理現場へのMES導入を検討している方も多いのではないでしょうか。
近年、少量多品種のニーズの高まりやリードタイムの短縮など、より生産管理の効率化が求められています。そんな中、作業者への指示や生産状況のリアルタイムデータの可視化など、生産管理の効率化に役立つMES(製造実行システム)が注目されています。
本記事では、MESを導入するメリットや注意点、他システムとの違いなどを徹底解説します。
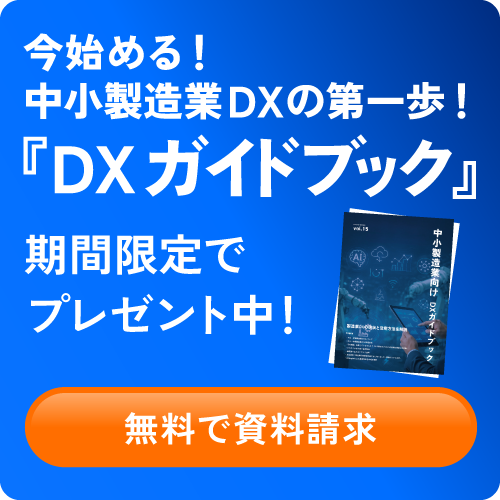
1. MES(製造実行システム)とは?
MESとは、「Manufacturing Execution System」の略で、「製造実行システム」と呼ばれます。
生産管理の中でも特に「工程管理」に特化しており、各工程の流れや連携を可視化・最適化します。
製造工程のリアルタイム情報を取得することで、生産効率向上やコスト削減を目指すシステムです。
具体的には、製造現場での業務に特化して、製造工程の可視化・製造現場の環境整備・作業者への指示などを行います。
MESの機能と立ち位置
MESは製造する製品の種類によって、必要な機能が異なります。
アメリカのMES推進団体であるMESAが提唱する、MESに搭載されている11の機能をご紹介します。
機能 | 内容 | |
1 | 生産資源の配分と監視 | 設備や工具、人材など生産活動に必要な資源を配分し監視する |
2 | 仕様・文書管理 | 図面や指示書、BOMなど生産に必要な文書を編集・管理する |
3 | 作業のスケジューリング | 生産計画に基づいたスケジュールの作成やシフトの作成・管理を行う |
4 | 差立・製造指示 | 最適な作業フローを立案し、作業員へ指示する |
5 | 作業者管理 | 作業状況の監視や、作業の割り当てを最適化する |
6 | 工程管理 | 生産状況を監視し、プロセス制御や、例外状況におけるアラートなどを行う |
7 | データ収集 | 各工程での進捗状況や実績など、生産に関連するデータを収集・分析する |
8 | 製品の追跡と体系管理 | 仕掛品の追跡や後工程を管理する |
9 | 実績分析 | 過去データを参照して生産状況を分析し、レポート作成や進捗管理を行う |
10 | 品質管理 | リアルタイムでデータ分析し、品質管理を行う |
11 | 保守・保全管理 | 設備・工具の保全や、予防保全のスケジュールを作成・実行する |
製造業で活用される管理システムには、「計画層」「実行層」「制御層」の3つに分かれます。
MESは「実行層」に位置し、製造工程の管理がメインとなります。
各層で代表的なシステムは以下です。
・計画層:EPR(企業資源計画)
・実行層:MES(製造実行システム)、MOM(製造オペレーション管理システム)
・制御層:SCADA(監視制御システム)、PLC(シーケンサ)、DCS(分散制御システム)
生産計画全体を管理する計画層と、生産現場の各工程である実行層、生産設備の稼働管理・制御を行う制御層それぞれの階層は互いに連携します。
MESの必要性
近年、昔ながらの大量生産では多様化する消費者ニーズに応えることが難しくなっています。
そのため少量多品種の生産や製造量の調節、需要量を予測し在庫数を最小限に抑える「需要調整型」など、多様化するニーズに臨機応変に応えられる、適切な生産管理が求められています。
また、国内外の競合製造業と戦うためには、DX化の推進や人手不足解消などの対策は不可欠です。
製造工程を可視化し、属人化させない適切な工程管理が可能となるため、MESは効率化に有効な製造業システムとして注目されています。
2. MES・生産管理システム・ERPの違い
前述の通り生産管理で活用されるシステムは、「計画層」「実行層」「制御層」の3層にわかれ、MESの他に「生産管理システム」「EPR(企業資源計画)」などがあります。
いずれも生産管理をサポートするシステムですが、目的や機能、対応範囲が異なります。
MESと生産管理システムの違い
生産管理システムは受注から納品までのデータ管理・分析・生産計画立案などを効率化するシステムです。その対象業務は多岐に渡ります。
つまり「生産管理システム」とは生産管理全般(3層すべて)の情報を管理します。
一方でMESは、生産管理システムの一部です。
生産管理の中でも工程管理(製造を実行する)に特化して、生産ラインを効率よく進めるための機能が備わっています。
MESとERPの違い
ERPとは、Enterprise Resource Planningの略で経営資源の一元管理を行います。
ERPは「計画層」に位置し、販売部門や会計部門などの業務実行、受注から出荷までの生産スケジュールを組みます。
「工程管理」に特化したMESと異なり、ERPは「ヒト・モノ・お金・情報」といった企業資源を管理します。
ERPで受注情報などを整理してMESで作業指示を行い、MESで得たデータをERPに渡すという連携が行われます。
3. 生産管理にMESを導入するメリット
MESを導入することで、生産管理が目指すQCDの最適化が期待できます。
MESを導入する具体的なメリットを4つご紹介します
生産性向上が期待できる
MESを導入すれば、部門間で正確な生産状況の情報の共有ができます。
部門間のスムーズな連携により、トラブルも抑制でき生産性の向上が期待できます。
さらに全国に複数拠点がある場合も、MESという同じシステムを使っていれば、急な仕様変更があった場合に各工程・各部門で迅速な対応が可能となります。
リアルタイムデータが活用でできる
不良品が発生した場合、原因が発生した工程の調査に時間がかかります。
MESでリアルタイムデータを活用できることで、自動収集された製造データから迅速に原因を特定し、対策に取り組むことができます。
製造現場の「今」を正確に共有できることで現場の業務改善につながり、短納期での納品を目指せます。
コスト削減が目指せる
工程管理のリアルタイムデータが活用できることで、非効率的な作業などをあぶりだし、生産管理の「ムダ」を排除できます。
ムダの排除により、業務が効率化できコスト削減が期待できるでしょう。
また、MESに蓄積されたデータから、製品1つ作るのにかかる原価を正確に算出できます。
実際にかかった原価と製造現場の状況を照らし合わせ、どうすれば原価を低減できるかの対策をとることができます。
トレーサビリティへの貢献
高い品質維持や、不良品流出時の迅速な対応のためには、生産の過程を追跡できるトレーサビリティが非常に重要です。
MESでは各工程の状況や実績を細かに分析できるため、トレーサビリティ確保に役立ちます。
トレーサビリティを確保することで、トラブル抑制や企業価値の向上が期待できます。
4. 生産管理にMESを導入する際の注意点
MESのメリットを解説してきましたが、導入する際にはいくつか注意する点もあります。
導入の目的を明確化する
MESを導入することで達成したい目的・解決したい課題は、各企業で異なります。
目的によってMESに必要な機能などが異なるため、目的を曖昧にすると導入後のトラブルにつながることもあります。
企業が目指す姿を達成するために、MES導入の目的を明確化し、社内に周知しましょう。
さらに、MESの要件を決める際には優先順位を決めることも重要です。
投入できる資金は有限であるため、解決したい課題の優先度を決めることで、予算内で段階的な課題解決が可能となります。
導入コストを考える
中小企業にとっては、MES導入・構築にかかるコストが大きな壁となることもあるでしょう。
導入コストがかかったとしても、同等もしくはそれ以上の価値を提供するMES・パートナー企業を選定する必要があります。
MES導入にかかるコストには以下が含まれます。
・初期費用
・ライセンス費用
・ランニングコスト(運用費)
・オプション費用
上記以外にも、「サブスクリプション型」などシステムを一定額で利用できる価格使用のものもあります。初期コストを削減できるなどのメリットがあります。
生産管理システム導入には『ものづくり補助金』が使える場合があります!
図面管理システム導入には『ものづくり補助金』が使える場合があります!
詳しくはこちらの記事で解説していますのでぜひご覧ください。
自社に合ったシステムを選定
すでに別システムを導入している場合、既存システムとのデータ連携・統合が可能なMESかは確認しておく必要があります。
さらに、MES実際に現場で利用する従業員への教育も必要です。
「現場の従業員がより活用しやすいインターフェース」
「自社に必要な機能が備わっている」
など自社に合うMESを選定することも重要です。
さらに、導入から運用・保守まで一気通貫で支援するベンダー企業の選定も、MESを長期的に活用していくためには重要です。
複数ベンダーを比較し、コストだけでなく機能や対応範囲まで調べて、自社のニーズに合うベンダーを選定しましょう。
5. MES導入のステップ
MES導入は、以下のステップで進めます。
①導入目的の設定
前述の通り、自社・チームにおけるMES導入の目的を明確化させます。
②MES導入プロジェクト発足・事前準備と体制作り
製造現場責任者など社内で適した人材を集め、MES導入のためのプロジェクトを発足するのをおすすめします。
事前準備をしっかり行うことで、MES導入がスムーズに進みます。
③MES選定・システム構築
目的に合わせて実際にベンダーやMESを選定します。
製造現場が抱える課題とその優先度、実際に投入できる人材とコストを洗い出し、総合的に比較して自社に合ったMESを選定します。
④導入後の運用・保守
せっかくMESを導入しても適切な活用・定着ができなければ意味がありません。
社内でしっかり活用して課題解決に向かっていけるよう、従業員への教育や現場の業務整理などを行う必要があります。
また、MESの導入方法は「パッケージ」「ハーフスクラッチ」「フルスクラッチ」の3つに分かれます。
パッケージ
パッケージとは、完成されたシステムを導入するためゼロから開発する必要がありません。
そのためコスト削減やスピーディーな導入が可能です。デメリットは、機能や仕様を自社に合わせてカスタマイズできない点です。
ハーフスクラッチ
ハーフスクラッチとは、パッケージシステム導入後に必要に応じて機能を追加するなどカスタマイズが可能な方法です。ベースはパッケージのため、コストを抑えつつ制限はありながらもある程度自由にカスタマイズできます。
フルスクラッチ
フルスクラッチとは。ゼロからシステム開発して導入する方法です。完全オリジナルで自社の要望を反映させることができます。高いコストと長い開発期間が必要ですが、導入後に高い効果を得られる可能性が高いです。
一般的な業務を行っている企業はパッケージ(もしくはハーフスクラッチ)、専門的で独自の業務を行っている企業はフルスクラッチ(もしくはハーフスクラッチ)での導入が多いでしょう。
ただし自社内での改善活動が活発な場合、製造現場の変化が激しいため、パッケージ製品ではフィットしない場合があります。
自社の状況に合った方法で導入することをおすすめします。
6. まとめ
MESを生産管理の現場に導入するメリットや注意点、導入の流れを解説しました。
MESは、生産管理の中でも「工程管理」に特化して情報管理・作業者への指示などを行うシステムです。
MESを導入することで生産管理の目指すQCDの最適化に貢献できますが、導入には大きなコストと事前準備、社内体制構築などが必要となります。
コスト面でMES導入をお悩みの方は、まずは図面管理システムを導入するのもおすすめです。
紙の図面をスキャンしていたり、過去図面の管理が煩雑化している企業では、図面管理を1つのシステムで統合的に管理・確認できるようにすることで、工数を大きく削減できます。
営業製作所では、図面をデータで一元管理できる「図面Engine」を提供しています。
図面Engineは、高いセキュリティの中で図面の取り込みや入力・データ化もすべて自動でできます。
生産管理現場の業務効率化を進めたい方は、ぜひ図面Engineの導入をご検討ください。