INDEX
製造業・生産管理に従事者にはQCDの最適化・改善が求められます。
しかし、実際にQCDについて詳しい人、QCDの最適化のために具体的に何をすればいいのか理解している人は少ないのではないでしょうか。
本記事では、生産管理で重要なQCDについてその最適化のポイントを解説します。
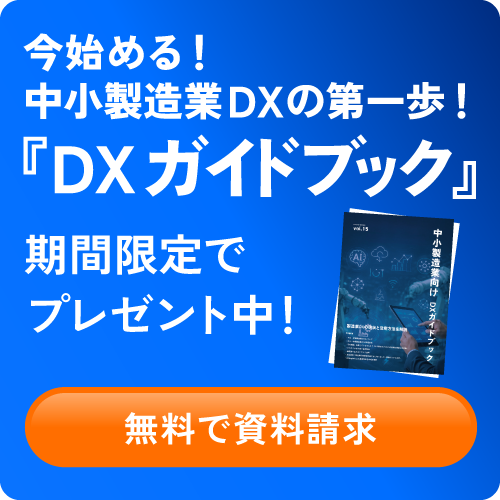
1. 製造業・生産管理のQCDとは?概念と重要性
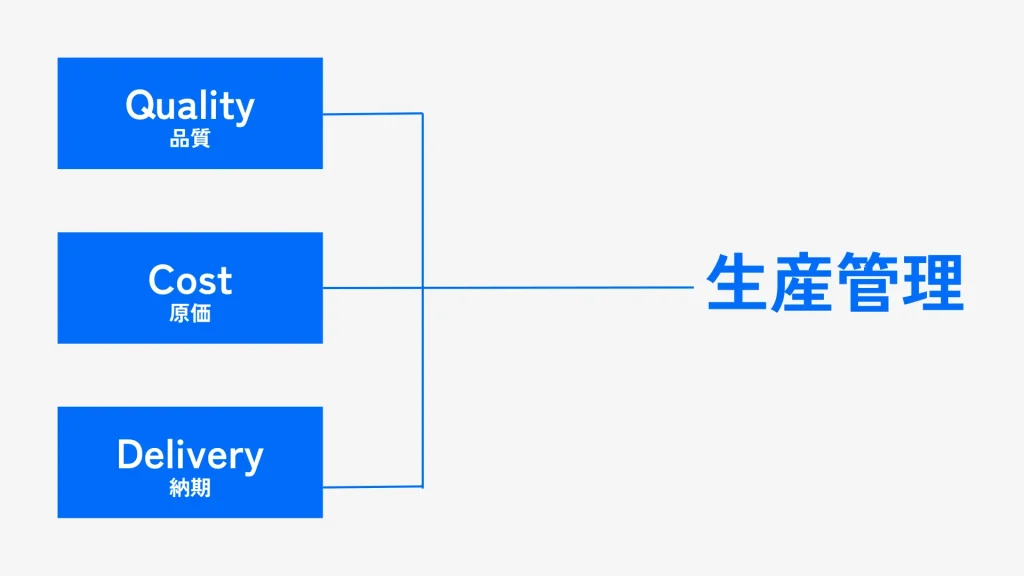
製造業・生産管理における「QCD」とは、「Quality(品質)」「Cost(コスト)」「Delivery(納期)」のことで、生産管理ではこの3要素を監督し継続的に改善していくことが求められます。
生産管理だけでなく製造業全体において、製品の品質向上など顧客満足に影響を与え、ビジネス全体の成長や競争力向上を支えます。
まずはQCDの理解を深めるために各要素について解説します。
1. QCDの要素(Quality, Cost, Delivery)
1. 品質(Quality)
– 定義:顧客の期待に応える製品品質を一貫して提供すること
– 具体例:不良品率0.1%以下の維持、顧客満足度90%以上の達成
2. コスト(Cost)
– 定義:利益を確保しつつ、競争力のある価格設定を可能にする製造コストの実現
– 具体例:原価率の前年比2%削減、設備稼働率95%以上の維持
3. 納期(Delivery)
– 定義:顧客との契約で定められた期日内に製品を確実に届けること、短納期で納品すること
– 具体例:納期遵守率99%以上の達成、リードタイムの20%短縮
2. 各要素の関係性
「Quality(品質)」「Cost(コスト)」「Delivery(納期)」の各要素は相関関係にあります。
以下のように1つの要素のみ注力してしまうと、他要素へ悪影響を与えるリスクがあります。
・品質のみ注力の場合
高品質を目指すと顧客満足度は向上する一方で、高品質を維持するためのコストが上昇します。また、品質チェックフェーズに力を入れると短納期での出荷が難しくなることがあります。
・コストのみ注力の場合
コストを抑えれば企業の利益率は向上しますが、安い材料を使うことによる品質低下や、人件費削減による納期遅延などが発生するリスクがあります。
・納期のみ注力の場合
短納期での出荷ができれば、顧客満足度は向上します。しかし品質が悪くなったり、納期短縮のために余計にコストがかかったりすることがあります。
このように、QCDは一つの要素に特化して改善するとそれ以外の要素でほころびが出てしまうことがあります。
そのためQCDの3要素すべてをバランスよく改善することが求められているのです。
3. 生産管理におけるQCDの重要性
QCD最適化がどのくらい生産管理において重要かを理解しておきましょう。
QCDの最適化が生産管理に与える良い影響は、具体的には以下が挙げられます。
・生産プロセスの改善、効率化
QCD最適化のためには、生産管理プロセスを受注管理~出荷までの一連の流れを見直し、改善する必要があります。
改善の内容としては以下があげられます。
・適切な需要予測・生産計画立案
・作業の標準化・自動化
・無駄や不良率の削減
生産管理プロセスを見直すことで、スピーディーな生産だけでなく品質のばらつきを抑え不良率改善にも貢献できます。
このようにQCDの3要素それぞれを改善していくことで生産プロセス全体の効率化につながり、企業の利益率向上にも貢献します。
・顧客満足度の向上
QCDの3要素どれを改善しても、顧客満足度の向上が期待できます。
高品質の製品を短納期で出荷し、さらに低コストでの生産を通じて低価格で製品を提供することができます。
顧客にとっては非常に大きなメリットとなるため、顧客はリピーターとなり長期的な関係を築くことができるでしょう。
・企業の差別化・ブランディングにつながる
QCDの最適化は、競合企業との差別化を図ることにもつながります。
ターゲットとなる顧客がQCDのうちどの要素を最も求めているかによって、自社の強みを強化していくと良いでしょう。
顧客のニーズを知ることで、自社を差別化し、ブランディング強化も可能となります。
既存顧客とは長期的な関係構築ができ、自社の強みを世間にアピールすれば新規顧客獲得も効率的に行うことができます。
注力内容としては、品質重視の顧客なら「品質改善」に注力する、低価格での取引を重視する顧客なら「原材料調達にかかるコストダウン」などが挙げられます。
自社の強みを強化し競合他社との優位性を浸透させることができれば、それは企業のブランド化すなわちブランディングにつながります。
2. QCD最適化の方法・ポイント
QCD最適化をスムーズに進めるためにはいくつかのポイントがあります。
1. QCD管理の3つのステップと管理方法
QCDをスムーズに改善していくためには、各要素を分断して改善していくことはおすすめしません。
「プロセス改善」として受注管理~出荷までの一連の生産管理プロセス全体を通して改善していくことがポイントです。
特に以下3つのステップで最適化を進めていきます。
①課題の把握
実際に現場で行われている生産工程の現状を把握します。
現場スタッフへのヒアリングの他、スケジュールや出荷数、実際にかかった工数など具体的な過去数値の分析を行いましょう。
課題を導き出したら、どの課題を最も優先的に対処すべきか優先順位をつけておきます。
②改善策の立案と実施
課題を把握できたら、具体的な改善策を立案し実施します。
具体的には「工程別の確認項目を増やし不良率を0.1%改善させる」「図面管理が煩雑であるため図面管理ツールを導入し図面管理コストを0.2%改善させる」などです。
改善案には、必ず達成する具体的な数値を記載しましょう。達成する具体的な数値を決めておくことで検証時に達成できたかできていないかを判断しやすくなります。
③検証、さらなる改善案立案
改善施策を実施したら、施策に効果があったか検証を行います。
改善案に記載した目標数値に対して達成できたか、達成できていなかった場合どの程度までは改善できたのかなど具体的に検証していきましょう。
達成できていなかった項目は、さらなる改善策を立案し、施策を実行していきます。
以上のように、現状把握を行ったのちに「改善計画立案→改善の実施→検証→さらなる改善の実施」と流れるサイクルは、「PDCAサイクル」と呼ばれます。
PDCAサイクルとは、「Plan(計画)」「Do(実行)」「Check(検証)」「Action(改善)」の頭文字をとったものです。
生産管理におけるQCDの最適化ではこのPDCAサイクルを継続的に回していくことが重要です。
2. QCDにおけるバランスの重要性
前述のように、QCDの3要素はバランスよく改善していくことが重要です。
特に以下の点に気を付けてQCDのバランスを意識していきましょう。
・トレードオフ(相関関係)の理解
前述のように、QCDの各要素は互いに影響しあうトレードオフの関係です。
1つの要素だけを優先すれば他要素が悪化してしまう可能性があるため、バランスよく改善しましょう。
・市場やニーズに合わせた柔軟な対応
消費者ニーズが多様化している現在、以前の大量生産方式ではニーズに対応できないことが増えました。そのため、在庫リスクを軽減するためにも少量多品種での生産方式が増えています。
生産する製品や出荷個数などは、市場の状況と顧客のニーズに合わせて柔軟に対応する必要があります。
QCD最適化も同じく柔軟な対応を行う必要があります。
例えば競合が増え価格競争が激化した場合、優先してコストを改善しながらも品質や納期も一定レベルを保つ努力が必要となります。
・継続的な改善活動
前述の通り、QCDの改善ではPDCAサイクルを回すことが重要です。
一時的な改善活動ではなく、小さなことでも継続的に改善活動を繰り返すことをおすすめします。
近年では、AI技術を活用したQCD最適化技術が発達してきています。
従来人力で行っていた作業をより効率的で的確に判断ができるAIに任せる事で、
さらに生産活動を改善される動きも見られています。
詳しくはこちらの記事で解説しています。ぜひ合わせてご覧ください。
3. QCD最適化の優先順位決定のポイント
QCD最適化では各要素のバランスが重要だと述べましたが、一般的には以下の優先順位がつけられる場合が多いです。
品質>納期>コスト
最も顧客満足度に影響を与える「品質ファースト」でのQCD最適化が基本です。
しかし、ビジネスの状況や先を見据えた戦略の内容によっては自社独自で優先順位を決める場合もあります。
優先順位決定のポイント
自社独自に優先順位を決める場合、以下のポイントに気を付けましょう。
生産管理やビジネスにおける目標を明確化する
まずは自社のビジネス目標を明確にしておきます。QCDの優先順位は必ず自社目標に沿う必要があります。
市場シェアを拡大したい場合はコストを優先し低価格での提供を目指す、ブランディングを強化したい場合は品質を優先する、などです。
顧客のニーズを理解する
顧客のニーズを理解することはQCDの優先順位を決める上で非常に重要です。
顧客の求めるものを理解し、それに合わせた優先順位とします。
3.競合の状況を把握
競合の現状や戦略、強み弱みを把握しておきましょう。
競合に弱みを自社で補完できれば、差別化を図ることができます。
4.内部リソースを把握
内部リソースを把握することで、QCDのどの要素を優先することが最も効率的で効果的か判断します。
資金に余裕のある場合投下できるリソースに余裕のある
5.リスク管理を行う
どの要素が改善のインパクトが大きいかということだけではなく、どの要素の悪化が「リスクが少ないか」という考え方も重要です。
例えば顧客満足度を重視する場合、「品質が落ちると顧客からの信頼を失うため品質を優先する」など、自社が最も避けたいリスクに対して対策を行う必要があります。
4. まとめ
今回は、生産管理求められるQCD(品質・コスト・納期)の最適化・改善活動について解説しました。
QCDの各要素は互いに影響しあうため、バランスよく継続的に改善していく必要があります。目的を明確化し、継続的にPDCAサイクルを回していくことが大切です。
QCD最適化のために生産管理システムなどの自動化ツールなどの導入を検討することもあるのではないでしょうか。
しかし、対応範囲の広い生産管理システムやERPの導入には、コスト面や導入準備にかかる工数などからハードルの高さを感じるかもしれません。
そのような場合、まずは煩雑になりがちな図面管理の効率化を進めることをおすすめします。
営業製作所では図面管理を効率化するシステム『図面Engine』を提供しています。
図面Engineでは、図面データの自動取り込みやAIによる自動入力、図面情報の一元化が可能となります。
QCD最適化の第一歩として、図面管理システムの導入を検討されてみてはいかがでしょうか。
詳しくは以下をご覧ください。
▼図面管理システムなら営業製作所の『図面Engine!』